Editor's Note: Take a look at our featured best practice, Training Needs Analysis (TNA) (72-slide PowerPoint presentation). Training Needs Analysis (TNA) goes beyond mere employee preferences or superficial surveys. It's a strategic process focused on aligning training with business objectives and bridging performance gaps.
This training PowerPoint will provide you with a comprehensive understanding of TNA, [read more]
Also, if you are interested in becoming an expert on Human Resource Management (HRM), take a look at Flevy's Human Resource Management (HRM) Frameworks offering here. This is a curated collection of best practice frameworks based on the thought leadership of leading consulting firms, academics, and recognized subject matter experts. By learning and applying these concepts, you can you stay ahead of the curve. Full details here.
* * * *
The Training Within Industry (TWI) program is one of the most popular approaches to developing the skills of experienced operators and leaders in instructing, improving and problem solving. One TWI method is TWI Job Instruction (JI), which is focused on conducting on-the-job training. This method is aimed at reducing the root causes of human errors, which include the following:
- Poor or no operator training
- Poorly prepared work standards that are not observed by operators
- A lack of control and audit systems for operators after trainings
Many companies use TWI JI to standardize their processes. For example, according to data presented at the Lean Enterprise Institute Conference, at the European division of Cooper Standard Automotive, all the plants that took part in the implementation of the TWI program in the first wave increased productivity by an average of 17.55 percent and reduced the level of deficiencies by an average of 35.83 percent.
The TWI JI method was mainly created to train employees in repetitive operations. However, the nature of production has changed, and there is a growing number of mixed model productions where the operator performs a number of different operations during his or her shift. The question now is how to standardize operations when there are, for example, 150 different references.
The answer is to list several leading product groups. For example, when we prepare a warm beverage, there may be two types of product groups: coffee and tea. These product groups can be prepared in many ways; these preparation methods are called references:
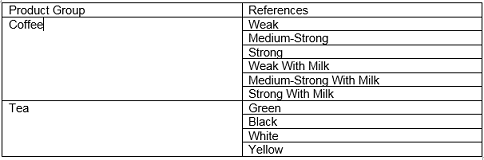
In the case of multi-variant production, a job breakdown sheet (JBS) should be prepared for each product group. A JBS is a tool for an instructor to use during on-the-job training and contributes to TWI work instructions. The JBS divides work into three categories:
- Major steps: logical segments of the operation in which something happens to advance the work
- Key points: anything that might make or break the job, injure the worker, or make the job easier to do
- Reasons for each key point
This table presents the JBS for the operation of preparing coffee:
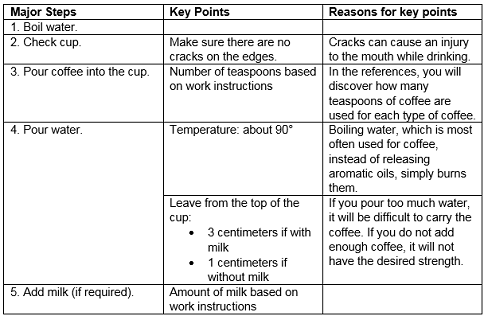
Each reference for a JBS should be accompanied by work instructions. In fact, the automotive industry requires them. Some of these instructions are very similar (e.g., preparing weak coffee with milk and preparing medium-strong coffee with milk).
Instructors should use a JBS for the specific product group when discussing the work during instruction. When they explain the major steps and key points, they should have the work instructions in hand. In the third major step of preparing a weak coffee with milk, for example, they should specify, based on the work instructions, that one flat teaspoon of coffee should be added. Similarly, when discussing the fifth major step, they should refer to the work instructions and tell learners that they should add milk to about 1 centimeter from the top of the cup.
This approach can be used in any process where multi-variant production exists. Many companies implement a lean management approach to reduce one of the most dangerous wastes: overproduction. The TWI approach to work standardization will translate into the elimination of human errors, which will in turn affect all key performance indicators.
129-slide PowerPoint presentation
The TWI Job Instruction (JI) program trains supervisors in how to instruct a person to perform a job correctly and safely; and to be productive as quickly as possible, while creating less scrap, rework, and damage to tools and equipment.
This tried and tested methodology is based on the
[read more]
Want to Achieve Excellence in Human Resource Management (HRM)?
Gain the knowledge and develop the expertise to become an expert in Human Resource Management (HRM). Our frameworks are based on the thought leadership of leading consulting firms, academics, and recognized subject matter experts. Click here for full details.
The purpose of Human Resources (HR) is to ensure our organization achieves success through our people. Without the right people in place—at all levels of the organization—we will never be able to execute our Strategy effectively.
This begs the question: Does your organization view HR as a support function or a strategic one? Research shows leading organizations leverage HR as a strategic function, one that both supports and drives the organization's Strategy. In fact, having strong HRM capabilities is a source of Competitive Advantage.
This has never been more true than right now in the Digital Age, as organizations must compete for specialized talent to drive forward their Digital Transformation Strategies. Beyond just hiring and selection, HR also plays the critical role in retaining talent—by keeping people engaged, motivated, and happy.
Learn about our Human Resource Management (HRM) Best Practice Frameworks here.
Readers of This Article Are Interested in These Resources
105-slide PowerPoint presentation
The TWI Job Methods (JM) program trains supervisors in how to improve the way jobs are performed in order to consistently produce greater quantities of quality products in less time using available manpower, machines and materials.
Participants are taught how to break down jobs into their
[read more]
24-slide PowerPoint presentation
The concept of Return on Investment (ROI) originated in the Manufacturing sector, where it's simple to measure time and output. Next to adopt the concept was the Banking industry, where it is used consistently. ROI calculation is now a common feature in every type, industry, and function of
[read more]
77-slide PowerPoint presentation
This is Module 7 of 8 of my popular Fundamentals of Change Management Course.
Module 7 contains 77 slides with the following 3 sessions:
- Session 1 "Training Management" - Describes all the necessary key activities needed to ensure people are adequately trained + a case study.
- Session 2
[read more]
97-slide PowerPoint presentation
The Training Within Industry (TWI) Job Relations (JR) program teaches supervisors how to evaluate and take proper actions to handle and to prevent people problems. This skill in leading helps the supervisor to improve his ability in working with people.
There are basic principles that,
[read more]