Editor's Note: Take a look at our featured best practice, Structured Problem Solving & Hypothesis Generation (34-slide PowerPoint presentation). This training PPT presentation provides a comprehensive approach to structured problem solving, starting with the identification of whether a problem or opportunity exists.
It guides you through pinpointing the exact location of the issue, understanding its root causes, and exploring potential [read more]
* * * *
“Continuous Improvement” is a term management consulting firms love using. It’s also a driving principle behind Lean Management.
So, how can we achieve Continuous Improvement in our organization?
One of the most common Lean frameworks for Continuous Improvement (of quality) is the Deming Cycle–also commonly known as PDCA Cycle, Deming Wheel, Shewhart Cycle, or Continuous Improvement Spiral. The Deming Cycle consists of a logical sequence of 4 repetitive steps for continuous improvement and learning: PLAN, DO, CHECK (STUDY), and ACT.
It originated in the 1920s with statistics expert Mr. Walter A. Shewhart, who introduced the concept of Plan, Do and See. Deming modified the cycle of Shewart towards: PLAN, DO, CHECK, and ACT. The Deming Cycle is related to Kaizen thinking and Just-in-Time (JIT) manufacturing. The concept of PDCA is based on the Scientific Method (which can be written as Hypothesis-Experiment-Evaluation-Do-Check), developed by Francis Bacon.
There is another version of this PDCA cycle is OPDCA. The added “O” stands for observation or as some versions say “Grasp the current condition.” This emphasis on observation and current condition has currency with Lean manufacturing/Toyota Production System literature.
There are numerous benefits to the Deming Cycle, spanning a variety of corporate functional areas. These include, but not limited to:
- Daily routine management-for the individual and/or the team
- The problem solving process
- Project management
- Continuous development
- Vendor development
- Human resources development
- New product development
- Process trials
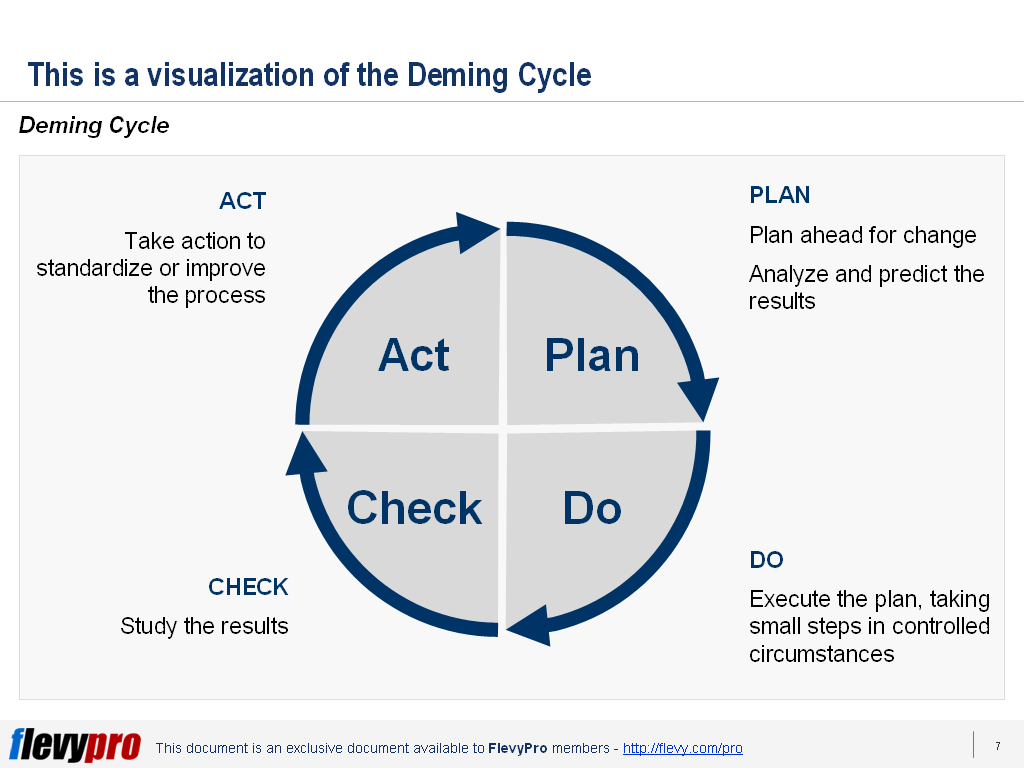
Here’s an overview of each of the 4 PDCA phases.
1. PLAN
This initial phase involves identifying a goal or purpose, formulating a theory, defining success metrics, and putting a plan into action. In this stage, we establish the objectives and processes necessary to deliver results in accordance with the expected output. By establishing output expectations, the completeness and accuracy of the specification is also a part of the targeted improvement.
2. DO
In the DO phase, the components of the plan are implemented (e.g. making a product). The focus is to implement the plan, execute the process, and ultimately make the product.
3. CHECK
Now, we study the actual results (measured and collected in DO) and compare against the expected results (targets or goals from the PLAN) to determine any differences. We look for deviations in implementation from the plan and also look for the appropriateness and completeness of the plan to enable the execution–i.e., “Do.”
4. ACT
If the CHECK shows that the PLAN that was implemented in DO is an improvement to the prior standard (baseline), then that becomes the new standard (baseline) for how the organization should ACT going forward (new standards are enACTed).
If the CHECK shows that the PLAN that was implemented in DO is not an improvement, then the existing standard (baseline) will remain in place.
In either case, if the CHECK showed something different than expected (whether better or worse), then there is some more learning to be done.
Note that the Deming Cycle is an iterative process, so after ACT, we return back to PLAN. Over time, we will achieve Continuous Improvement in quality. Each time we renew the cycle, our organization is at a higher point of quality. Executing the cycle again will extend our knowledge further.
For much more in-depth training guides and training on PDCA, take a look at Flevy’s PDCA Business Toolkit. Flevy also has developed several other related business toolkits:
You can learn more about this Lean tool and download in an editable PowerPoint about the the Deming Cycle here on the Flevy documents marketplace.
230-slide PowerPoint presentation
The PDCA cycle, also known as the Deming Cycle or the Shewhart cycle, is a four-step continuous improvement process that is widely used in quality management, business improvement, and project management.
The PDCA cycle is an iterative process, meaning that it is repeated continuously in order
[read more]
Do You Want to Implement Business Best Practices?
You can download in-depth presentations on Problem Solving and 100s of management topics from the FlevyPro Library. FlevyPro is trusted and utilized by 1000s of management consultants and corporate executives.
For even more best practices available on Flevy, have a look at our top 100 lists:
These best practices are of the same as those leveraged by top-tier management consulting firms, like McKinsey, BCG, Bain, and Accenture. Improve the growth and efficiency of your organization by utilizing these best practice frameworks, templates, and tools. Most were developed by seasoned executives and consultants with over 20+ years of experience.
Readers of This Article Are Interested in These Resources
88-slide PowerPoint presentation
Root Cause Analysis (RCA) is a problem-solving approach aimed at identifying the primary cause of a problem, ensuring that the issue is addressed at its source. By doing so, organizations can implement long-term solutions, enhance efficiency, lower costs, and improve customer
[read more]
206-slide PowerPoint presentation
The 8D Problem Solving Process has become a standard in many industries as problem solving or improvement process, as internal Corrective Action Request (CAR) Process or as Supplier Corrective Action Request (SCAR) Process.
The 8D Problem Solving Process Training Module includes:
1.
[read more]
32-slide PowerPoint presentation
According to McKinsey, structured problem solving can be used to address almost any complex challenge in business or public policy. Consulting deliverables typically take the form of PowerPoint presentations.
AIM:
1. This document explains how to identify, define and solve problems in a
[read more]
57-slide PowerPoint presentation
This document provides a practical guide to structured problem solving. It will help you solve strategic problems that your business face. The document provides a framework that has been tested for many years at a top tier consulting firm and investment bank. There are numerous examples given to
[read more]