Editor's Note: Take a look at our featured best practice, Total Productive Maintenance - 30 Templates (Excel workbook). This Excel workbook contains 30 templates for Total Productive maintenance ( TPM ) concepts. Templates include OPL ( One point Lesson) Gantt Chart, Why Why Analysis, Overall Inspection, Jishu Hozen Step - 4 , List of "Fuguai" in the Equipment, Why Why Because Logic [read more]
The Difference between Preventive vs. Predictive Maintenance
* * * *
When managing industrial equipment, you may agree that the maintenance of your assets is vital for your business. This is especially true when that equipment’s functionality can heavily impact your company’s efficiency and overall productivity. Alongside this, you’ll find that well-maintained machinery is highly cost-efficient as you won’t have to worry about unnecessary repairs that could’ve been prevented through thorough maintenance. Furthermore, well-maintained machinery will allow you to develop high-quality products that perform well. This is where understanding what condition monitoring is and how this is a critical aspect of predictive maintenance, comes into play.
That said, if you’re reading this, you may be developing or hoping to improve your maintenance strategy by reading about preventive and predictive maintenance. Preventive maintenance can be referred to as maintenance that is routine, planned, and scheduled. Therefore, it is done regularly at intervals. Meanwhile, predictive maintenance can be seen as more of a condition-based kind of maintenance. This means that it’s more focused on performing maintenance activities and schedules when your software indicates that it is necessary.
While you may simply choose between either type of maintenance, using both may also be worth considering. Overall, it really depends on what you need and how much you’re willing to pay. As such, it’s essential to know which one you need for a particular case scenario and exactly what they can do. With this in mind, here are the differences between preventive and predictive maintenance:
What You’ll Need to Perform the Maintenance
The difference between the two will be the costs, software, and machine downtime involved in them. For one, preventive is known to have a low overall investment cost compared to predictive maintenance. This is because predictive, on top of personnel and checklists, requires a special kind of software and tools and sensors to detect any issues with your machinery.
Next, when it comes to software, preventive is known to use maintenance software for managing and maintaining equipment. Meanwhile, predictive maintenance uses condition monitoring software to keep a live feed on how your machinery is doing. With that, if you’re hoping to look for an example of maintenance software, you may want to consider one provided by 60Hertz or other service providers.
When Do You Need to Do the Maintenance
Another main difference between preventive and predictive maintenance is how often they’re done. For instance, as mentioned, prevention is done regularly, and it’s scheduled and planned regardless of whether your machinery has any damage or not.
On the other hand, predictive maintenance is only done when needed, as you’ll only perform maintenance activities when your software dictates that one is due. More specifically, the software involved with predictive maintenance will tell you when there is a failure or issue.
From here, you can either perform a maintenance activity immediately to address it or do so on the next scheduled maintenance activity. As such, you may actually use both preventive and predictive together.
Advantages
Another difference worth considering between these two types of maintenance is their advantages. You may take the following advantages as an example:
Preventive
- It prolongs the machine’s lifespan as you regularly maintain them.
- Increased employee and customer safety because you won’t wait for any issues to arise.
- It’s efficient, especially when you have very skilled personnel.
Predictive
- It immediately identifies issues, allowing them to be fixed before a machine failure happens.
- You can just buy parts that need to be replaced and not those still working, making it cost-efficient and even time efficient.
- You can discover more efficient maintenance practices using the data collection involved in predictive maintenance.
Disadvantages
With that, it’s also worth considering the following disadvantages of these types of maintenance:
Preventive
- You may replace a part or perform a repair when it’s not yet needed, making it unnecessarily costly and time-consuming.
- It also requires more investment and time to make sure that you perform maintenance regularly.
- It requires more effort for inventory management for replacement parts.
Predictive
- The investment costs are higher as you’ll have to pay for extra equipment and software.
- It can get in the way of planned projects as it’s focused on detecting and addressing issues only when they appear.
- It can result in failing equipment which can consume more energy and time since this is focused on detecting and addressing issues instead of preventing them.
Conclusion
Maintenance is a core part of preserving product quality, overall safety, productivity, and efficiency. As such, it’s important to devise a maintenance management plan for your equipment to especially avoid paying for repairs that could have been avoided. With this in mind, in devising a maintenance management strategy, it’s essential to know preventive and predictive maintenance.
However, it’s worth noting that you may use both of these together for a more effective maintenance strategy. This is especially since predictive can identify issues that need to be addressed for the next scheduled maintenance. Therefore, it may not have to be a case of choosing between them but thoroughly understanding which is best used for a certain case scenario. That said, hopefully, the guide above has helped you gain a deeper understanding of the difference between preventive and predictive maintenance.
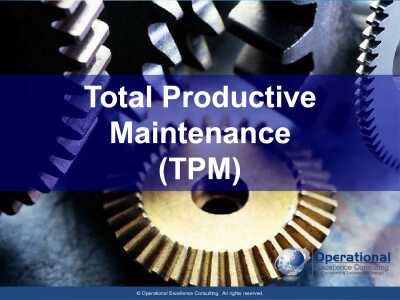
Do You Want to Implement Business Best Practices?
You can download in-depth presentations on TPM and 100s of management topics from the FlevyPro Library. FlevyPro is trusted and utilized by 1000s of management consultants and corporate executives.
For even more best practices available on Flevy, have a look at our top 100 lists:
- Top 100 in Strategy & Transformation
- Top 100 in Digital Transformation
- Top 100 in Operational Excellence
- Top 100 in Organization & Change
- Top 100 Management Consulting Frameworks
These best practices are of the same as those leveraged by top-tier management consulting firms, like McKinsey, BCG, Bain, and Accenture. Improve the growth and efficiency of your organization by utilizing these best practice frameworks, templates, and tools. Most were developed by seasoned executives and consultants with over 20+ years of experience.
Readers of This Article Are Interested in These Resources
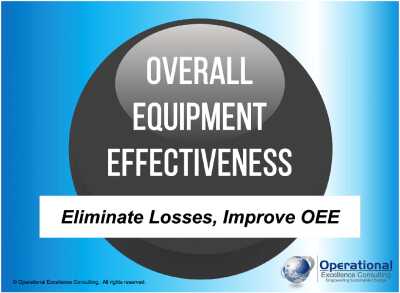
|
208-slide PowerPoint presentation
|
|
57-slide PowerPoint presentation
| |||
About Shane Avron
Shane Avron is a freelance writer, specializing in business, general management, enterprise software, and digital technologies. In addition to Flevy, Shane's articles have appeared in Huffington Post, Forbes Magazine, among other business journals.
Top 10 Recommended Documents on TPM
» View more resources TPM here.
» View the Top 100 Best Practices on Flevy.
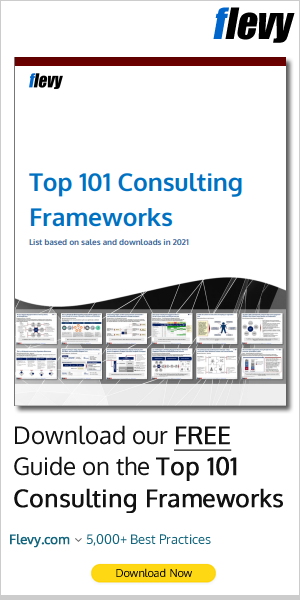