Editor's Note: Take a look at our featured best practice, Trucking / Delivery Business Financial Model (Excel workbook). If you are trying to validate your trucking business (or a general delivery business), this 5-year financial model is just the right tool. These assumptions were specifically designed to meet the needs of a trucking business whose primary revenue stream is from making deliveries. Here is a [read more]
Six Challenges Associated with Reverse Logistics… and How to Overcome Them
Also, if you are interested in becoming an expert on Supply Chain Management (SCM), take a look at Flevy's Supply Chain Management (SCM) Frameworks offering here. This is a curated collection of best practice frameworks based on the thought leadership of leading consulting firms, academics, and recognized subject matter experts. By learning and applying these concepts, you can you stay ahead of the curve. Full details here.
* * * *
In basic terms, reverse logistics is about moving products backward through your supply chain.
It can involve returning goods to suppliers, redistributing items to customers or retailers, and recycling or disposing of products.
Reverse logistics can create multiple challenges, so check out the following six challenges and how you can overcome them.
1. Streamlining Return Order Flows
Return order flows can be complex. They require coordination with multiple partners in your supply chain.
And when items are returned for processing, those products need to be inspected, verified, and tested. Products could need to be repaired and repackaged too. Also, decisions will need to be made as to whether it is more cost-effective to recycle or scrap raw materials rather than refurbish defective products.
Therefore, it can be challenging to streamline return order flows because reverse logistics involves so many variables.
To overcome the complexities of return order flows, you should integrate structured processes and systems and use management software to provide you with holistic planning and execution, which should include end-to-end visibility.
2. Ensuring You Have Enough Warehouse Space
Dealing with reverse logistics means you need to have additional space in your warehouse for products that need to be sent back through the supply chain.
But without a high level of organization, you could find you do not have enough space in your warehouse.
You should monitor how many goods, on average, you need to send back to suppliers, to recycling centers, and so on, each month, so you can determine how much additional space you require.
Then, ensure you have a designated area in your warehouse for processing items that need to go through the reverse logistics process.
You may need to readdress the layout of your warehouse and make on-the-ground changes in order to create the extra space you need.
3. Lowering the Cost and Time It Takes to Process Damaged Items
When a big part of your reverse logistics operation involves handling damaged items, it will cost you a lot of time and money. In turn, that can significantly impact your bottom line.
To overcome the problems, ensure you have well-rounded returns policies in place and you utilize an effective inventory management system.
4. Ensuring Customers Are Not Missing Crucial Information for the Products They Purchase
Damaged products are just some of the items that are returned by customers. Other products that are commonly returned are ones that are missing important information, even when those items are fully functional.
For instance, consumers often send back electrical items that are missing technical specifications.
This is one of the easiest challenges in reverse logistics to overcome. You simply need to ensure the products that you sell are always accompanied by the right information.
That begins with selecting the right products to sell.
You can also help your customers to make more informed buying decisions by providing detailed inventory catalogs and product guides online.
5. Avoiding Costs Incurred by Customer Dishonesty
Some of your returned products will be sent back by customers who are dishonest and use tactics to try and get something for nothing.
But you can reduce the amount of customer fraud by implementing a carefully thought out returns policy that has restrictions.
For example, by simply having designated cut-off times for returning items, you could significantly cut down reverse logistics losses.
6. Reducing Carbon Emissions
In this day and age, most companies are finding ways of being eco-friendlier and more sustainable in their operations, but reverse logistics can create more carbon emissions, as items need to be redistributed throughout the supply chain.
To overcome an increased carbon footprint, and thereby reduce carbon emissions, your company should adopt green supply chain solutions such as repurposing returned items, using zero-waste packaging and utilizing environmentally friendly methods for the disposal of the items that need to be discarded.
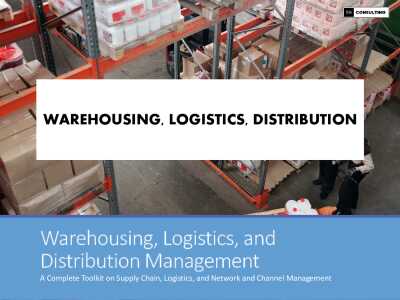
Want to Achieve Excellence in Supply Chain Management (SCM)?
Gain the knowledge and develop the expertise to become an expert in Supply Chain Management (SCM). Our frameworks are based on the thought leadership of leading consulting firms, academics, and recognized subject matter experts. Click here for full details.
Supply Chain Management (SCM) is the design, planning, execution, control, and monitoring of Supply Chain activities. It also captures the management of the flow of goods and services.
In February of 2020, COVID-19 disrupted—and in many cases halted—global Supply Chains, revealing just how fragile they have become. By April, many countries experienced declines of over 40% in domestic and international trade.
COVID-19 has likewise changed how Supply Chain Executives approach and think about SCM. In the pre-COVID-19 era of globalization, the objective was to be Lean and Cost-effective. In the post-COVID-19 world, companies must now focus on making their Supply Chains Resilient, Agile, and Smart. Additional trends include Digitization, Sustainability, and Manufacturing Reshoring.
Learn about our Supply Chain Management (SCM) Best Practice Frameworks here.
Readers of This Article Are Interested in These Resources
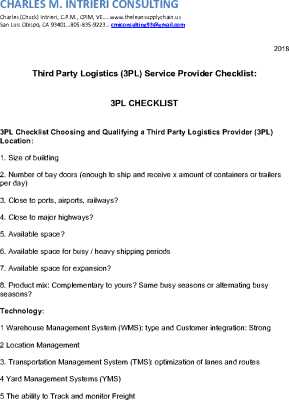
|
Excel workbook
|
|
Excel workbook
| |||
About Shane Avron
Shane Avron is a freelance writer, specializing in business, general management, enterprise software, and digital technologies. In addition to Flevy, Shane's articles have appeared in Huffington Post, Forbes Magazine, among other business journals.
Top 10 Recommended Documents on Logistics
» View more resources Logistics here.
» View the Top 100 Best Practices on Flevy.
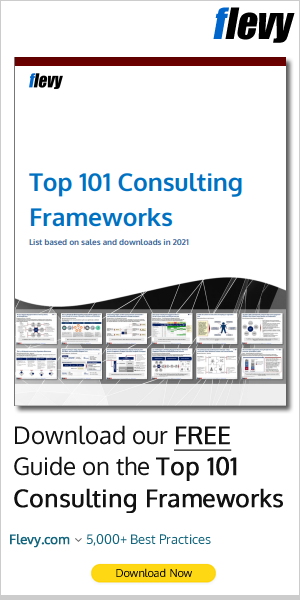